MOBIL CHEMICAL COMPANY
1987 - 1992
Pictures of the facility in Jacksonville, Illinois made in
2006 (now belongs to Pactiv):
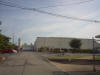
West Site |
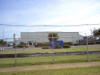
West Site |
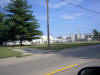
West Site |
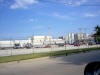
West Site |
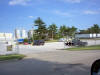
West Site |
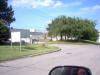
West Site |
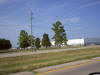
East Site |
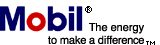 |
Mobil brought me into the world of robotics and packaging automation.
After interviewing at Mobil I was assigned to what would become the Machine
Development Group of the Consumer Products Division. The Consumer Products Division
manufactured Hefty, Kordite, and many private label brands of garbage bags. The
Machine Development Group consisted of a mechanical engineer, a chemical engineer, an
electrical engineer, and three technicians. We designed equipment, assisted
start-ups, and provided troubleshooting to plants in Washington, NJ, Temple, TX, and
Jacksonville, IL. While we lived and held primary offices in Jacksonville, Illinois,
we reported to our division headquarters in Macedon, NY. We were responsible for the
division machine projects that ranged from automating existing equipment to developing new
processes. I designed circuits and wrote programs for blown film extruders, bag
machines, packaging machines, case packers, and conveyors.
One of my biggest projects was the automation of the Mainstream Bag
Machines. Our job was to replace the humans that manually packed the bags into
boxes. We had to replace their eyes and their ears. One of my proudest
accomplishments was some really nifty logic that I thought of one night in the
shower. This logic would locate a defect on a single bag and reject it while the
line continued to run at several hundred feet per minute.
We would build the prototype on a working machine in Jacksonville,
Illinois. We then called in the management in all the plants to show off our work,
which included work plans and drawings (on AutoCAD). Basically, we sold the project.
If the plant wanted our work then we submitted a request for capital funding.
When approved, our project went to Central Engineering for installation. We
worked with Central Engineering as the OEM (even though we were Mobil engineers). We
then went into the various facilities to inspect and start up the equipment. We then
trained the operators and technicians. Finally we retained responsibility as the
last line of defense for troubleshooting equipment (similar to most OEMs).
At the time we had forty-four bag machines that we upgraded with PLCs,
drives, and lots of photoeyes and solenoids. We kept the boys at Allen-Bradley,
Reliance, Banner, and Turck happy.
Some of my other memorable projects were installing Cinch Sak in
Washington, rewriting the Jones Machine program and developing a coupon dispenser. I
also assisted as we installed a LAN in Jacksonville.
One of my fun roles was traveling once a year to Macedon, NY to provide
training to the benchstrength engineers. My task was to introduce them to the world
of automation. It allowed me a first-hand glance at the oncoming engineering staff
in all the Mobil Chemical Plastics and Consumer Products facilities.
I also got to act as liason to the Foams Group. This role allowed me
new experiences in working with controls in the Mobil foams facilities.
We spent many hours on the road and in hotels. Clyde, a technician,
and I played pool many nights at Sassy Sam's in Temple, Texas and spent many weekends at
work keeping the projects moving.
In 1991 our work in the MDG was complete. I transferred to the Films
Division as a Sr. Systems Engineer for a plant start-up in LaGrange, Georgia. The
new position would move me back to the sunny South.
LaGrange was an experience in itself. We started up two 8.4 meter
oriented polypropolene lines and the associated equipment. My responsibility
included everything from the winders on the orienters to the shipping docks. One of
the most interesting aspects of the job was working with the OEMs. Mobil had bought
equipment from around the world and I worked with people from Japan, Italy, France,
England, and Germany. Many of them could barely speak English if they spoke it at
all..
In LaGrange we had many various forms of Siemens, Toshiba, Telemecanique,
Allen-Bradley, and Square D PLCs. We also had a menagerie of drives including
Reliance, Siemens, Allen-Bradley, and many other "off-brands". The primary
control in the facility was maintained by ABB DCS systems. Wow! We absorbed a
lot to get that place going.
I remember walking into the plant as the Japanese completed work on one of
the 8.4 meter winders. They were leaving in two weeks and could not speak much
English. We had a translator out of Atlanta. The equipment included a Toshiba
EX2000 which, at the time, was extremely rare in the states. I quickly fell into a
constant learning mode after the Japanese left. They were on the other side of the
world and at the opposite end of the time spectrum. Our best mode of communication
with them was by fax. But, we managed to keep the line running.
In late 1991 Cindy's grandmother became ill and lived with us for several
months. Finally, in September of 1992 I took a job with Avery Dennison in Peachtree
City. My office would be located across the street from Cindy's grandmother's house.
Mobil was a great company. We got to see the world and work with
many of the Mobil facilities around the country. Today Tenneco Packaging owns what I
used to know as the Consumer Products Division, Plastics Packaging Division, and the Foams
Division. I still have many friends at both Mobil and Tenneco.
|